SCAFFOLDING SAFETY: 5 STEPS TO TAKE BEFORE ERECTING SCAFFOLDING
July 1, 2019
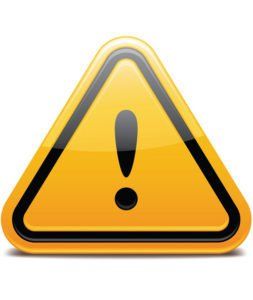
Everyday, dozens or even hundreds of people – friends and coworkers, beloved sons, daughters, fathers, and mothers – trust their lives and their livelihoods to safe and effective scaffolding solutions.
Scaffolding safety is of prime importance. By definition, these movable, adjustable, customizable construction tools can either prevent or cause dangerous conditions at the job site, depending on how well they function, and how they are used.
On-the-job hazards, close calls, or faulty equipment can have a dramatic impact on productivity and profit. Unsafe conditions not only reduce the enthusiasm of workers on the job site, but can also cause an accident to evolve into a costly lawsuit or workers’ compensation claim.
A holistic approach to scaffolding safety on the job site must take into account external threats, visitors, and the surrounding environment. Here are five steps to proactively create a safe job site before erecting scaffolding.
1. Get the Proper Equipment
Proper equipment is essential to set your job site up for success. Make sure to invest in high-quality Personal Protective Equipment (PPE), including:
- Hardhats with straps to prevent losing the hardhat while elevated.
- Gloves that allow dexterity while not sacrificing protection.
- High Vis apparel rather than vests that may get snagged on equipment during erecting and dismantling (E&D).
- Fall Protection such as retractable lifelines with steel cable vs synthetic lanyards as they are less prone to abrasion and possible fraying.
In addition, plan to take an extra step and provide a few extras to enhance safety, such as supplying:
- Lanyards for wrenches and hammers to prevent overhead tool loss and ‘Struck by’ incidents.
- Torque Wrenches vs. Standard Ratchets to prevent overstressing the equipment and thus reduce damage to structure components.
2. Evaluate Site Conditions
Ground conditions must be evaluated to ensure an adequate E&D process can proceed. However, geotechnical concerns like erosion potential or a high water table are not seen by the naked eye.
In addition, if you are working on industrial or multi-craft sites, coordinate with nearby trades before erection begins to ensure:
- No overhead work is being performed (e.g. cranes, manlifts, overhead structures or mezzanines, etc.). If so, guard against struck by hazards.
- No blasting is planned that may compromise E&D or structure post erection.
- No nearby excavations are happening, which could compromise soil or base
3. Create a Field Level Risk Assessment (FLRA)
A field level risk assessment (FLRA) is used to examine operational and procedural systems on a daily basis to identify hazards that may be necessary to protect workers at a site. By completing a FLRA prior to any work being done on site, possible risks and hazards are identified early and procedures can be put in place to suggest ways for controlling risks and keeping the site safe. It may include the use of some forms or checklists such as:
- Process of erection, which can minimize the hazards associated with the overall process
- Bracing plan
- Material Handling procedures
- Power lines
- Inclement weather
- Loading Capacity for occupants throughout E&D as well as use. For example, will the structure be sufficient for the intended purpose? Does the structure meet criteria where it would need to be ‘engineered’ vs erected by a competent person?
- Establish ‘Pass Line’ and methods of communication for materials to be hoisted and lowered
4. Create a Rescue Plan
A rescue plan should be mapped out for workers to refer to throughout the E&D process. Creating this before erecting scaffolding gives you time to add the proper materials to your inventory to have them on hand in the case of an emergency.
5. TRAIN, TRAIN, TRAIN your staff
When OSHA revised scaffolding safety standards in 1996, studies by the Bureau of Labor Statistics found that 25% of workers involved in scaffolding accidents
had not received safety training. As a manager, you can reduce the risk for your crew by conducting proper OSHA and equipment-specific safety training. OSHA training is designed to protect employees from common hazards such as falls, falling objects, structural instability, and overloading.
Beyond OSHA requirements, make sure to document all of the steps above and share it with your crew before erection begins. Once the job is underway, make sure to reevaluate these safety measures and continue to customize and adapt based on site needs.
Read this article
for additional scaffolding safety tips once your job site is active and underway.
You might also like
AT-PAC Blog
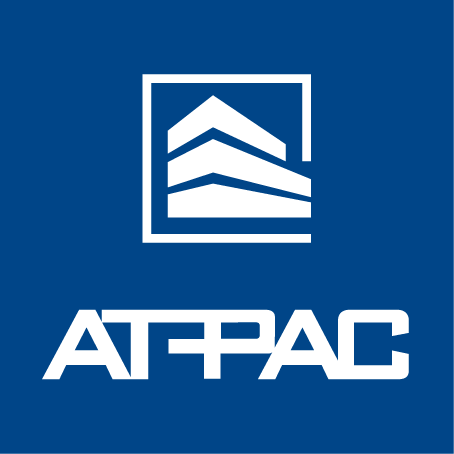
We are excited to share an important milestone in our journey. AT-PAC is now officially operating under umdasch Industrial Solutions. This transition further strengthens our position as an end-to-end scaffolding provider, expanding our reach and enhancing our ability to serve i ndustrial customers and scaffolding contractors worldwide.
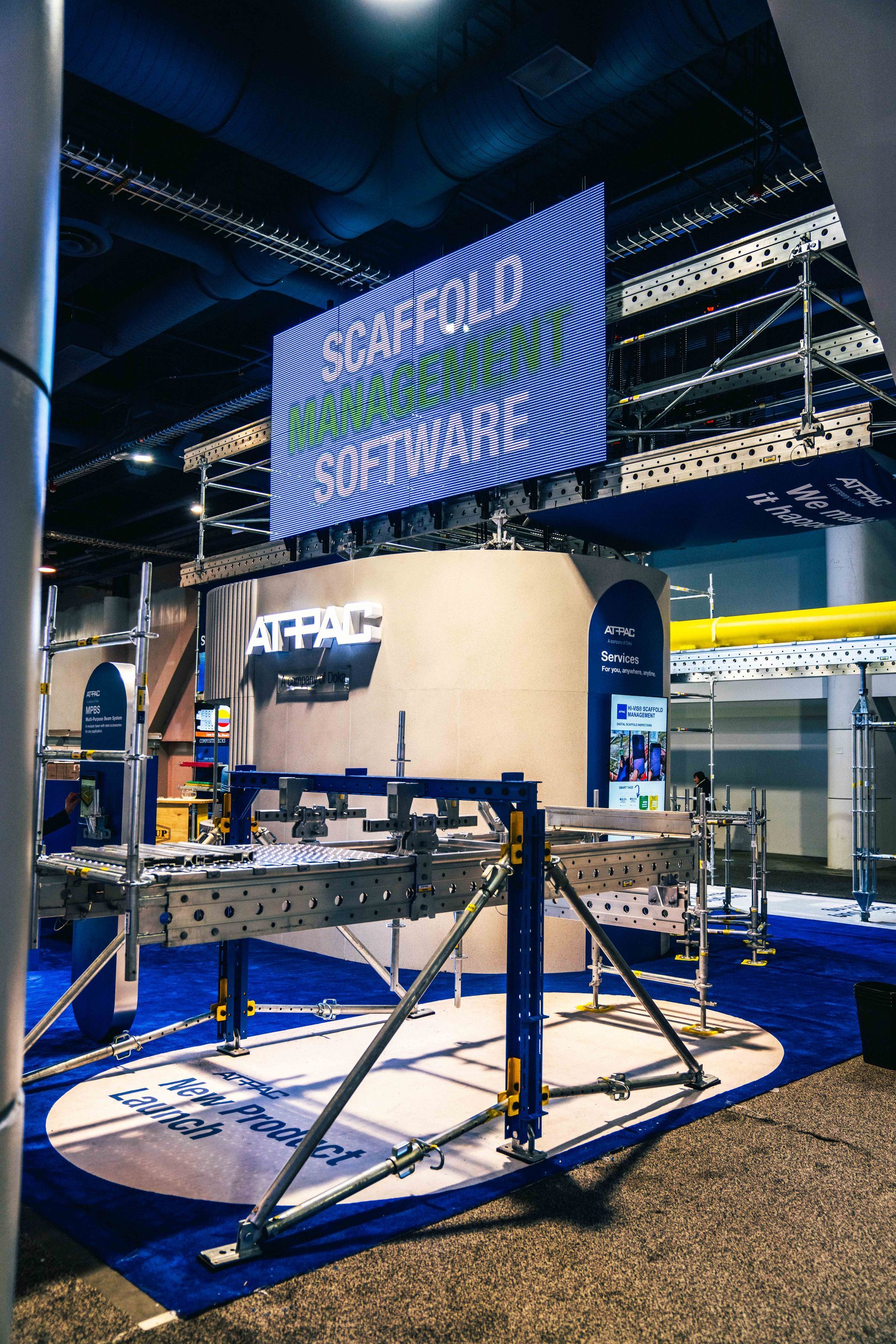
AT-PAC Unveils the Multi-Purpose Beam System (MPBS) at World of Concrete 2024 AT-PAC proudly launched its latest innovation, the Multi-Purpose Beam System (MPBS), at World of Concrete 2024, marking a significant milestone in scaffold technology. As a cutting-edge addition to AT-PAC’s proprietary Ringlock System Scaffold, the MPBS offers unparalleled versatility and efficiency, revolutionizing the way scaffold structures are designed and deployed. A Game-Changer for the Industry Designed to expand the capabilities of the Ringlock System, the MPBS provides a groundbreaking solution for a wide range of applications, including: Suspended Scaffold & Pipe Rack Scaffolds – Enabling safe and efficient suspended access solutions. Birdcages – Creating stable, large-scale work platforms. Large Span Bridging – Allowing for expansive scaffold spans with fewer components. Boiler Scaffolds – Meeting the unique needs of confined and high-heat environments. Cantilevers – Offering extended reach and accessibility. Innovative Design & Seamless Integration The MPBS system is engineered for simplicity and adaptability. At its core is a robust extruded aluminum beam, capable of supporting O-Type Ringlock Planks and an array of attachable steel accessories. With 6-inch (152.4mm) on-center attachment points along its length, the MPBS ensures maximum flexibility, making it suitable for diverse scaffolding applications. What sets the MPBS apart is its seamless integration into the Ringlock System, enhancing functionality while minimizing complexity. The ability to achieve larger spans than traditional methods reduces the overall number of components required, streamlining both installation time and labor costs.