WHY USE RINGLOCK SCAFFOLDING SYSTEM IN A COAL HOPPER?
July 11, 2019
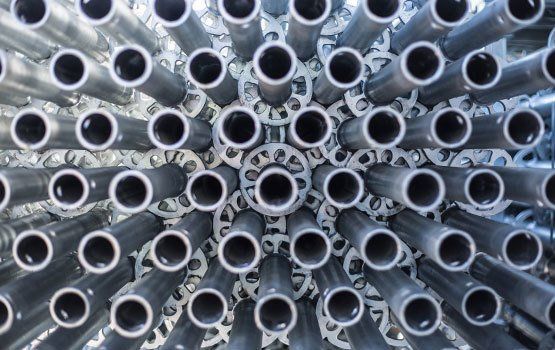
Thermal power plant managers must oversee the operations of a number of critical areas. Ensuring proper and adequate coal storage is just one of those responsibilities. However, when it comes time to construct a new coal hopper, or clean and service an existing hopper, extra resources are needed. That is where Ringlock Scaffolding System
comes in.
The versatility of the Ringlock Scaffolding System
Ringlock Scaffolding
boasts incredible versatility and can be built to suit any shape or size container or project. That is particularly useful in coal hoppers, which can often be awkward to work around and in. No matter the size of the access, you can get Ringlock Scaffolding Systems into a coal hopper.
In addition to versatility, Ringlock Scaffolding Systems also allow users to quickly and efficiently erect, use, and dismantle temporary work structures. This creates increased efficiency and productivity at a plant, and saves time and money by keeping operations on time and on budget.
How to erect the Ringlock Scaffolding System in tight spaces
Coal hoppers are traditionally built with a slope that feeds coal into a chute. Before erecting scaffolding inside the hopper, planks, or beams (wood planks for a brick hopper, base beams for a steel hopper) need to be secured to the wall so workers can climb the slope. Think of the planks as a makeshift ladder. Because the chute may run five to 20 feet deep into boilers, you also need to secure a lifeline or slack line for workers to attach themselves too.
Once you have taken the proper safety steps, you can begin erecting the scaffolding with this process:
- Start at the center line of the hopper and create a square base that will fit in the bottom, usually three 3×3 feet to 4×4 feet.
- Since the slope is very steep, start stepping out in all four directions with small bays for ease of erection.
- Place Swiveljacks on the slope.
- Place steel tubes to brace legs from sliding down the slope.
- Work your way out to the hopper walls to create planked working levels.
- Finish to the top of the hopper.
Ringlock meets or exceeds the highest American and European safety and durability standards. AT-PAC has manufactured the Ringlock Scaffolding System
and associated components since 1995 and we maintain distribution warehouses all over the world, which saves you both time and money.
Call our closest regional office or contact us online when you’re ready to integrate the Ringlock Scaffolding System into your power plant.
You might also like
AT-PAC Blog
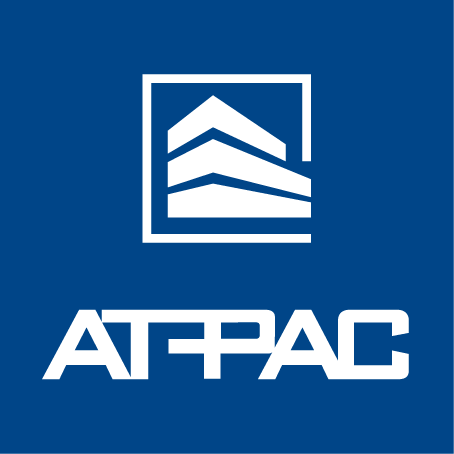
We are excited to share an important milestone in our journey. AT-PAC is now officially operating under umdasch Industrial Solutions. This transition further strengthens our position as an end-to-end scaffolding provider, expanding our reach and enhancing our ability to serve i ndustrial customers and scaffolding contractors worldwide.
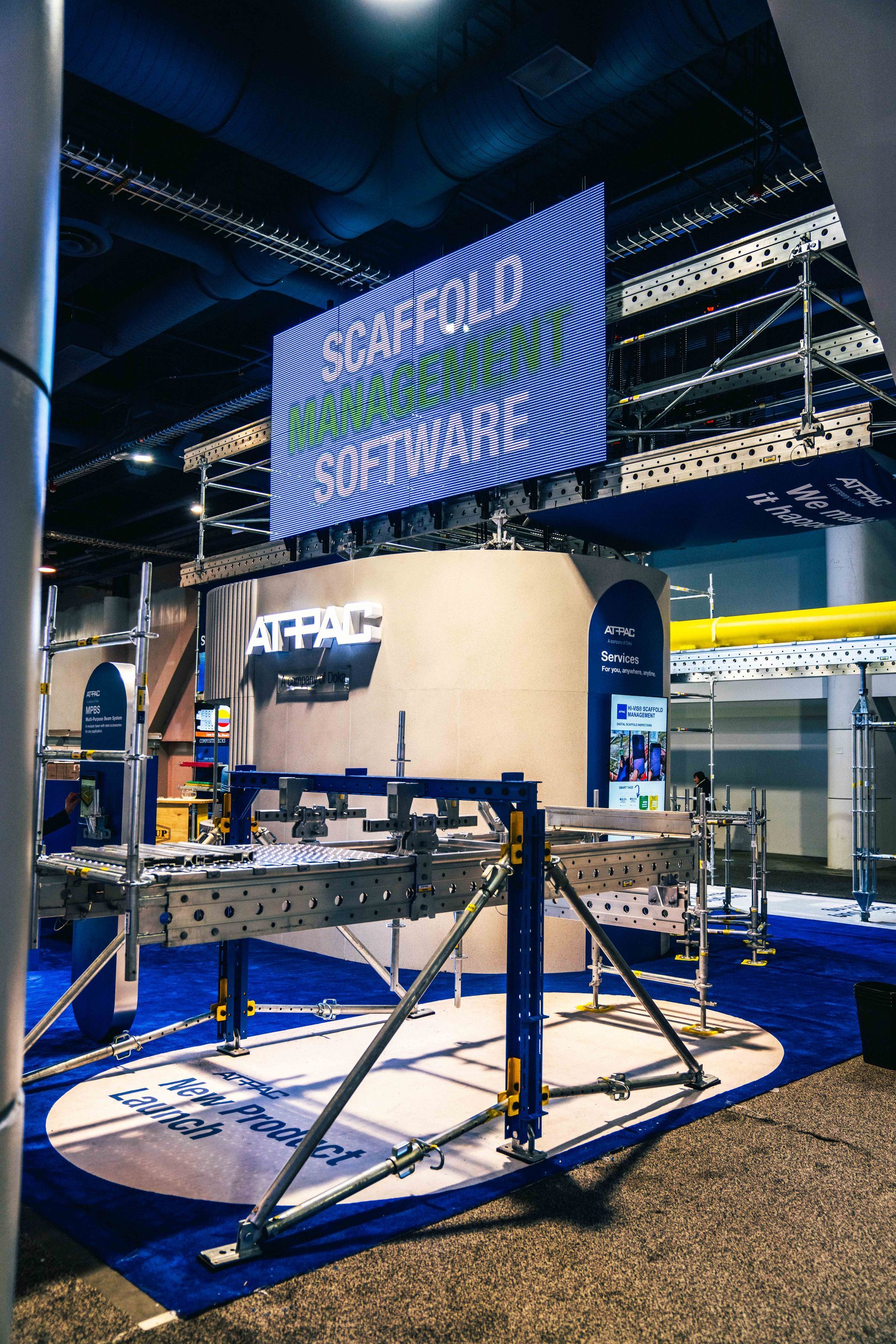
AT-PAC Unveils the Multi-Purpose Beam System (MPBS) at World of Concrete 2024 AT-PAC proudly launched its latest innovation, the Multi-Purpose Beam System (MPBS), at World of Concrete 2024, marking a significant milestone in scaffold technology. As a cutting-edge addition to AT-PAC’s proprietary Ringlock System Scaffold, the MPBS offers unparalleled versatility and efficiency, revolutionizing the way scaffold structures are designed and deployed. A Game-Changer for the Industry Designed to expand the capabilities of the Ringlock System, the MPBS provides a groundbreaking solution for a wide range of applications, including: Suspended Scaffold & Pipe Rack Scaffolds – Enabling safe and efficient suspended access solutions. Birdcages – Creating stable, large-scale work platforms. Large Span Bridging – Allowing for expansive scaffold spans with fewer components. Boiler Scaffolds – Meeting the unique needs of confined and high-heat environments. Cantilevers – Offering extended reach and accessibility. Innovative Design & Seamless Integration The MPBS system is engineered for simplicity and adaptability. At its core is a robust extruded aluminum beam, capable of supporting O-Type Ringlock Planks and an array of attachable steel accessories. With 6-inch (152.4mm) on-center attachment points along its length, the MPBS ensures maximum flexibility, making it suitable for diverse scaffolding applications. What sets the MPBS apart is its seamless integration into the Ringlock System, enhancing functionality while minimizing complexity. The ability to achieve larger spans than traditional methods reduces the overall number of components required, streamlining both installation time and labor costs.